Woodworking automation equipment really cares about everyone's needs and thinks about everyone's thoughts. At present, it is difficult to find workers, and even more skilled workers are even more difficult. For furniture companies under the market economy, if they do not use equipment, it will undoubtedly lead to self-destruction by closing the country. Orders in the furniture industry show a trend of large volume, tight delivery, low profits, and high competitiveness. In furniture production, the least efficient and most complicated thing is the processing of special-shaped workpieces. This is a common problem faced by furniture factories, and this problem is solved by CNC sawing and milling machines! CNC cutting machines are mainly designed and developed for complex special-shaped workpieces such as curved wood and special-shaped wood. Such as bedside components, dining chair components, etc.
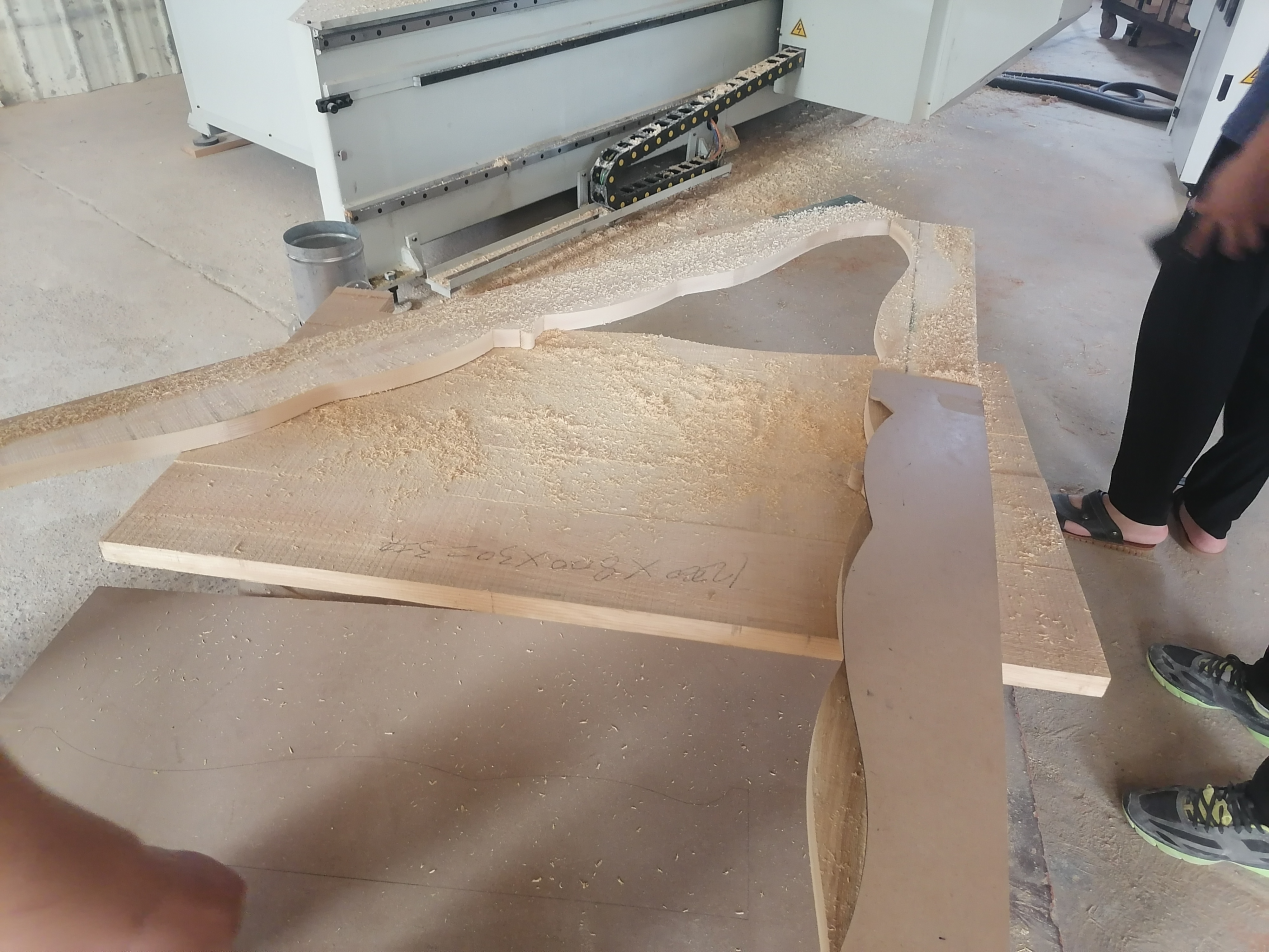
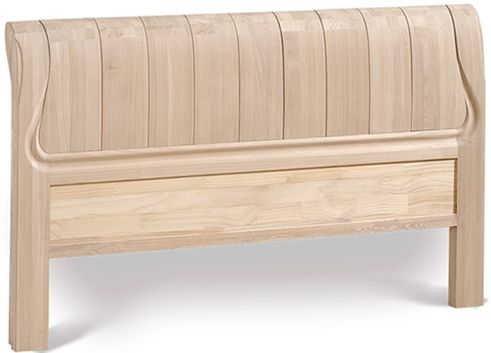
Regarding the mechanical characteristics, let’s do some related technical analysis:
The processing mode is a 6 mm or 8 mm spiral milling cutter, which adopts the upper and lower double-end clamping method, which will be more reliable, durable and not easy to break.
For processing loss, generally use a milling cutter of 6 to 8 mm. It should not be too thin. If it is too thin, the cutter will break easily. After all, the material of the milling cutter is hard, brittle, and sharp. This loss is completely acceptable, because the loss of the entire processing process using traditional processing methods will not be very low.
The processing efficiency is generally controlled at a thickness of 150mm. This thickness is equivalent to processing multiple layers of plates together, doubling the efficiency. And the speed can be accelerated or decelerated according to the specific situation.
Processing accuracy + quality, processing accuracy and quality are equivalent to vertical axis end milling. We all know that the traditional method is to cut out the shape and then perform end milling to mill out the excess rough parts. This is not processed by CNC sawing and milling machines, it will be standard after processing, smooth and beautiful. Processing cutter breakage rate, this cutter breakage rate is actually a problem that everyone is concerned about. For a long time, furniture factories have had the idea of processing wood and cutting wood through milling cutters. And preliminary tests have also been carried out. For example, the four-step cutting machine of the engraving machine is processed through the form of a milling cutter. However, the disadvantage is also obvious that the diameter of the cutter is at least larger than 10mm, which causes large losses, and even some cutters have to be used. 12mm or 14 or 16mm, which results in extremely serious wood loss. At the same time, the processing thickness is not large, which is 50mm. Even so, the tool is severely damaged and has a very high breakage rate. The new design clamps the milling cutter at both upper and lower ends, which virtually increases the fixing strength and stability, strengthens the milling cutter, and achieves a breakthrough in service life.
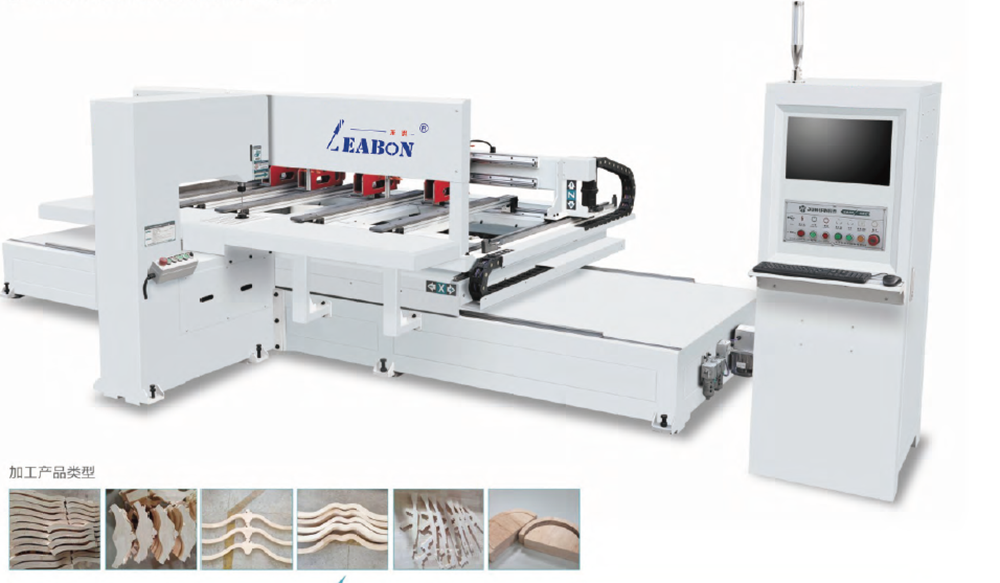
After comprehensive evaluation, this type of equipment is worthy of use and investment in daily production. In the long run, from many aspects such as saving labor, improving efficiency and technology, reducing risk factors to ensure work safety, merging technology to reduce expenses, etc., it is calculated and very cost-effective. I also hope that our technology and scientific research practitioners can make further progress in creating more, better and more advanced automation equipment to serve domestic enterprises and industries.
Post time: Nov-03-2023